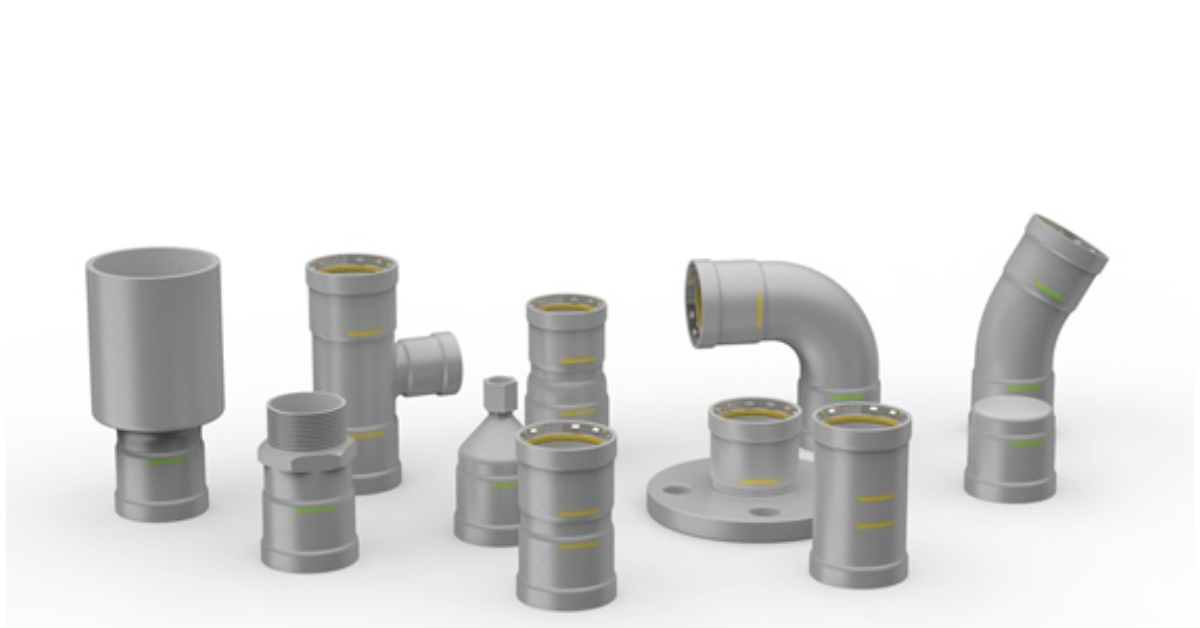
In the labyrinth of modern plumbing and pipeline systems, the importance of connections cannot be overstated. These junctures are pivotal to the integrity and functionality of the entire system, acting as the veins through which fluids flow. Enter engineered fittings – the unsung heroes ensuring durability, efficiency, and safety in plumbing and pipe works. This deep dive into engineered fittings illuminates their significance, types, benefits, and considerations for selection, offering a guide to achieving optimal connections in various applications.
The Critical Role of Engineered Fittings
Engineered fittings are designed to join pipe sections, manage directional changes, reduce or expand diameters, and facilitate system access for maintenance or inspection. Unlike standard fittings, engineered variants are tailored for specific applications, considering factors such as pressure, fluid type, environmental conditions, and regulatory requirements. This customization ensures that each fitting performs optimally under the intended operating conditions.
Types of Engineered Fittings
The realm of engineered fittings is vast, encompassing a variety of types each suited to particular needs:
- Elbows: Facilitate directional changes, available in angles like 45° and 90°.
- Tees and Crosses: Enable the connection of three or four pipes, respectively, often used to integrate branches into main lines.
- Reducers and Expanders: Adjust the pipe diameter to manage flow rates and accommodate pipes of different sizes.
- Couplings: Join two pipes of the same diameter, crucial for extending or repairing sections.
- Flanges: Provide a method for assembling and disassembling pipeline sections, useful for system maintenance.
Each type serves a unique purpose, contributing to the system’s overall efficacy and reliability.
Benefits of Engineered Fittings
Opting for engineered fittings over generic options brings numerous advantages:
Enhanced System Performance
Custom-engineered fittings are optimized for the specific parameters of a project, leading to improved system performance. They ensure smooth flow dynamics, minimize pressure drops, and effectively handle the intended fluid types and volumes.
Increased Durability
Materials and designs are selected based on the operational environment, resulting in fittings that are resistant to wear, corrosion, and failure. This longevity is critical in applications where reliability is paramount, such as in water supply, gas distribution, and industrial processing systems.
Safety and Compliance
Engineered fittings adhere to stringent safety standards and regulatory requirements, minimizing the risk of leaks, ruptures, and environmental harm. This compliance is essential in industries subject to heavy regulation, like oil and gas, chemical manufacturing, and pharmaceuticals.
Considerations for Selecting Engineered Fittings
Choosing the right engineered fitting involves several critical considerations:
- Material Compatibility: The fitting material must be compatible with the fluid type, temperature, and pressure conditions. Common materials include PVC, CPVC, stainless steel, and brass, each offering different advantages.
- Pressure Ratings: Fittings must withstand the system’s maximum operating pressure to prevent failures.
- Connection Type: The method of connecting the fittings to the pipes (threaded, welded, flanged, etc.) impacts installation ease and system integrity.
- Regulatory Standards: Ensure the fittings meet all relevant industry standards and certifications, which can vary depending on the application and location.
Custom Hose & Fittings: Tailored Solutions for Complex Systems
In addition to engineered pipe fittings, custom hose and fittings play a crucial role in complex plumbing and pipeline systems. These components are designed to meet the unique demands of applications that require flexibility, specific chemical resistances, or unusual temperature and pressure ranges.
Custom hoses, coupled with precisely engineered fittings, ensure a seamless flow and connection between disparate parts of a system, accommodating movements and aligning with specific operational requirements. This section will explore the importance of custom hose and fittings, their applications, and key considerations for their selection and use.
Future Trends in Engineered Fittings
The evolution of engineered fittings is closely tied to advancements in material science, manufacturing techniques, and digitalization. Developments like 3D printing offer new possibilities for custom fitting designs, enabling even more precise tailoring to specific system requirements. Additionally, smart fittings equipped with sensors are emerging, capable of monitoring system performance and predicting maintenance needs, further enhancing system reliability and efficiency.
Engineered fittings stand at the core of effective plumbing and piping systems, providing the crucial connections that ensure fluid flows smoothly and safely from point A to point B. Their design and material composition are meticulously tailored to meet the exact needs of each application, offering unmatched performance, durability, and safety. By carefully selecting the appropriate engineered fittings and considering future trends and advancements, professionals can achieve optimal connections that stand the test of time. In the vast network of pipelines that power our industries, communities, and daily lives, engineered fittings are the essential links that keep the flow uninterrupted and efficient, proving that sometimes, it’s the smallest components that make the biggest difference.